Supply Chain Management
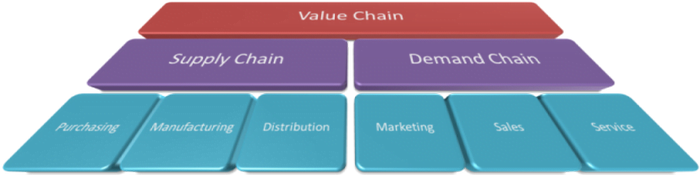
Supply Chain Management (SCM) is the active management of supply chain activities to maximize customer value and achieve sustainable competitive advantage. It is the management of the flow of goods and services, involves the movement and storage of raw materials, of work-in-process inventory and of finished goods from point of origin to point of consumption.
Within the Value Chain at least in terms of Supply Chain activities (to maximize customer value and achieve sustainable competitive advantage), the supply chain responsible often must account for both the supply chain as well as the Demand Chain all the while corresponding competencies were not extensively allocated.
Learn More About The Demand Chain
The demand chain is an essential concept that encompasses the processes and activities involved in satisfying customer needs. It is crucial for businesses to comprehend how this chain works to enhance their operational efficiency and meet market demands effectively. The demand chain extends beyond the traditional supply chain, focusing on value creation based on customer insights.
At the heart of the demand chain lies the significance of understanding customer preferences and behaviors. Companies that leverage customer insights can adapt their strategies accordingly, ensuring that products and services align with consumer expectations. This dynamic approach not only fosters customer satisfaction but also drives brand loyalty, ultimately benefiting the organization’s bottom line.
In conclusion, the demand chain serves as a pivotal framework for organizations aiming to excel in a competitive landscape. As businesses prioritize customer engagement and adaptive strategies, the demand chain will continue to evolve. By recognizing the importance of adapting to shifting consumer demands, organizations can effectively optimize their processes, minimize waste, and improve profitability. Embracing the demand chain philosophy is essential for future success, as it aligns operational goals with customer-centric approaches.
Corporate management includes key functions like supply chain (procurement for Profit), marketing & sales (driving Revenue), and supporting services. Organizations could benefit from dedicated roles also in Demand Chain or even Value Chain management, fostering strategic alignment and efficiency beyond traditional Supply Chain management.
“One might very well look into the possibility of creating ground for demand chain or even value chain responsibles for the sake of a healthy mix of competencies and responsibilities.”
– Eric Roth
Material Inventory & Logistics
Material inventory and logistics are fundamental to supply chain management, working together to ensure seamless operations and efficiency.
- Material Inventory manages raw materials, components, and finished goods for production and distribution, balancing availability with cost control to prevent shortages or excess stock.
- Logistics, on the other hand, coordinates the movement, storage, and transportation of these materials, ensuring timely deliveries and optimal resource utilization.
When integrated effectively, material inventory and logistics optimize supply chains, boosting productivity, reducing waste, and ensuring goods are available at the right place, time, and condition to enhance customer satisfaction.
Material Inventory
The Latin word “inventarium” translates to “Inventory” or “Stock” referring to goods a business holds for resale or repair. Inventory management within supply chain management (SCM) minimizes costs and maximizes satisfaction by maintaining optimal inventory levels and avoiding overstocking or stockouts. Integrating inventory control with SCM enhances forecasting, resource allocation, and efficiency, ensuring faster delivery and improved customer satisfaction.
Procurement
Procurement is the process of obtaining goods or services usually on a relatively large scale. Often confused with purchasing – or even buying – procurement represents a more strategic, sustainable and less purely transactional process.
There is a lot of literature and out-of-experience knowledge out there but yet, in daily business life, one encounters a very common misunderstanding of the terms Procurement, Purchasing and Buying. Whilst the first two are mostly B2B undertakings, the latter may be a B2C process as well.
Inventory Management
Inventory Management, a key part of supply chain management, involves overseeing ordering, storage, and product availability. The goal is to have the right inventory at the right quantity, quality, place, time, and cost.
- Stock the right amount of inventory.
- Pay the right amount for your inventory (Economic Order Quantity).
- Know your reorder point.
- Ensure you have the right amount of inventory in the right place.
Materials Management
Materials Management ensures an organization is supplied with the necessary goods and services for purchasing, storage, and material movement, primarily for production, while inventory management specifies the size and placement of stocked goods
ABC / XYZ Analysis
In materials management, ABC Analysis (or Selective Inventory Control) categorizes inventory into three groups. XYZ Analysis classifies inventory based on demand variability.
ABC Aanalysis
- “A items” being the most valuable ones with with highest demand and very tight control as well as accurate records.
- “B items” with less value, medium demand and tightly controlled as well as goods records.
- “C items“, the least valuable ones and low demand with the simplest controls possible and minimal records.
XYZ Analysis
- “X items“: Very little variation. Characterised by steady turnover over time. Future demand can be reliably forecast.
- “Y items“: Some variation: Although demand is not steady, variability in demand can be predicted to an extent. This is usually because demand fluctuations are caused by known factors, such as seasonality, product lifecycles, competitor action or economic factors. It’s more difficult to forecast demand accurately.
- “Z items“: The most variation. Demand can fluctuate strongly or occur sporadically. There is no trend or predictable causal factors, making reliable demand forecasting impossible.
Inventory Control
Inventory Control, including warehouse management, tracks stock accurately to support production, sales, and maintenance with minimal inventory, maximizing profits while ensuring customer satisfaction.
- Keep track of the stock that is already in the warehouse. This includes knowing what products are being stocked and how much of a particular item is available.
- Aspects of warehousing designs, such as knowing where everything is and ensuring that the products are stored well.
Reorder Point (ROP)
Reorder materials before stock runs out, but timing is crucial—ordering too early increases storage costs, while ordering too late risks disappointing customers and losing business.
- Lead Time Demand + Safety Stock = Reorder Point
Lead time demand is found by multiplying lead time by average daily sales. Lead time refers to the time from placing an order to receiving it – don’t confuse it with delivery time!
KANBAN
Meaning “signboard” in Chinese and Japanese, Kanban is an inventory system for supply chains. Let’s explore its six rules and their role in traditional production, JIT manufacturing, and knowledge work:
- Never Pass Defective Products • Take Only What’s Needed • Produce Exact Quantity • Level the Production • Fine-tune Production / Process Optimization • Stabilize and Rationalize the Process
Logistics
Supply chain management involves a network of external partners – vendors, transportation providers, call centers, and warehouses – working together to deliver products to customers. Logistics, however, focuses on internal company activities like purchasing, packaging, shipping, and distribution.
Logistics manages goods from origin to consumption, ensuring efficiency and meeting customer or corporate needs. It optimizes transportation, warehousing, and inventory control, reducing costs while enhancing customer satisfaction. A strong logistics system streamlines supply chains and boosts adaptability in dynamic markets.
Ninja Services
Pragmatic, Professional engagement rooted in global experience – Ninja services to navigate complexity, optimize operations and drive results through Value Creation.
My Background includes well-developed, solid Core Competencies and is available to address diverse business needs, ensuring exceptional outcomes. It provides tailored solutions for both assignments and roles with the flexibility for global travel.
Contact me today for effective support in navigating challenges and driving success.
What’s More
The posts in My Blog explore reflective and narrative-driven themes, often tied to personal experiences or societal observations, emphasizing storytelling and commentary.
Dependence (10) Fiction (10) Karma (10) Landmarks (10) Paramount (10) Spectrum (10) Spotlight (10) Take Off (9) Terra Shapes (9) Trepidation (9) Unique (10) Virtue (9)
Selecting an option will take you to that post.
(116
)
The topics in My Interests examine broad, conceptual, and philosophical ideas, emphasizing exploration of abstract notions and their deeper cultural and societal implications.
Amazing Stuff (9) Beyond Known (10) Controversial (9) Digital World (10) Inequities (10) Innovative (10) Metaphysics (9) Orbiting Entities (10) Our Society (10) Outer Space (10) Value Creation (10) Yearnings (10)
Selecting an option will take you to that post.
(117
)
Curious to dive deeper and ready to share your thoughts on all of this? Join the conversation and be part of the Site Forum. Your online discussion board providing space for engaging exchanges on specific topics and shared interests across this website.